ER1100 aluminum MIG welding wire
Author: Time:2023-05-17
ER1100 is a pure aluminum core wire, coating for base type aluminum strip. The strength of the welded
joint is not high, but the corrosion resistance is good, so the aluminum and aluminum alloy is not high
for the joint strength. DC power supply, welding electwiree, short arc welding. Arc stability is poor, the
splash is big.
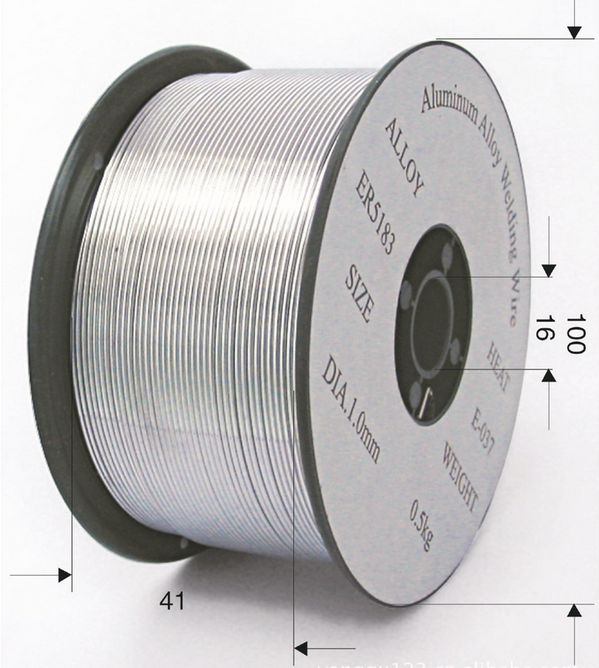
for the joint strength. DC power supply, welding electwiree, short arc welding. Arc stability is poor, the
splash is big.
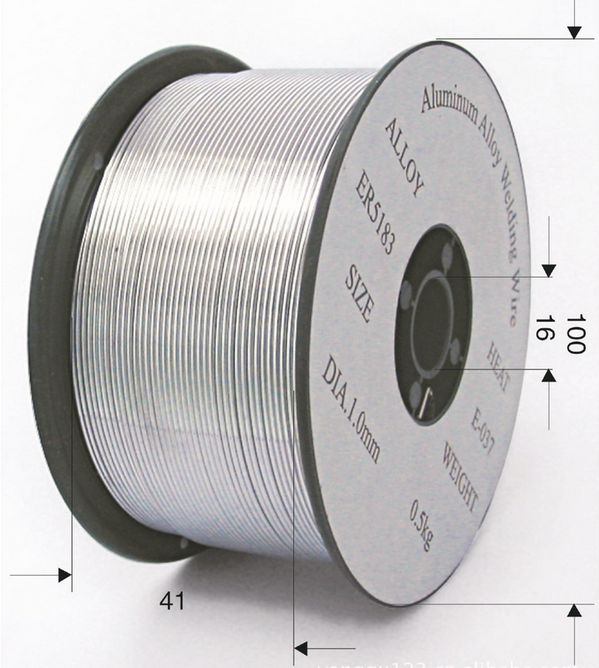
Uses: mainly used for welding aluminum, aluminum container.
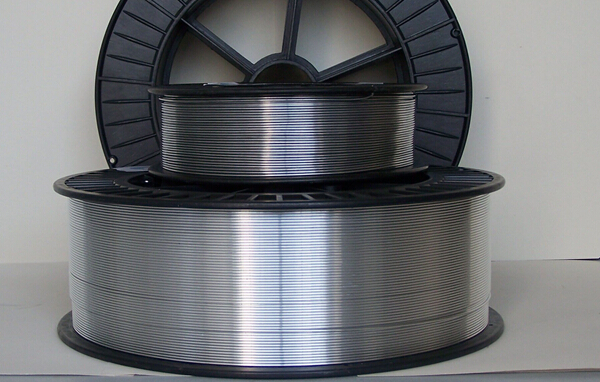
Mechanical Properties (reference value) | ||
---|---|---|
Item | Tension Strength(MPa) | Cold bending angle D=2T |
Standard | ≥80 | - |
Result | 80-90 | 180 |
Reference current: DC+ | |||
---|---|---|---|
Welding wire Diameter(mm) | 3.2 | 4.0 | 5.0 |
Welding Current(A) | 80--110 | 110--150 | 150--200 |
ER1100 Aluminium & Aluminium Alloy welding wires | |
Classification | GB/T 10858-2008 AWS A5.10 ···· ER 1100 |
Typical composition in % |
Si+Fe················ <0.95 Cu················· 0.05—0.20 Mn················· <0.05 Zn·················· <0.10 Be·················· <0.0008 Al·················· Remaining |
Physical properties (Approx.Values) |
0.2% yield strength Rpo2 (Mpa)····· 25 Tensile Strength Rm (Mpa)······ 80 Elongation A5 (L0=5d0) (%)···· 25 Test Temperature (℃)······ 20 |
Performance & Usage |
This type containing 0.05—0.2% copper and more than 99% Al.It has advantages ranges over good anti-corrosiveness,well electrical conductivity and processiveness . And it’s also a kind of best choice for color-match after anodic process.Recommended type:aluminium alloy 1000 . Usage:engine, electric power, chemistry ,food.etc . |
Shielding gas | Argon, Helium, or Argon/Helium—mixtures. |
Dimensions Φ |
MIG—wires (mm): 0.8 ; 0.9 ; 1.0 ; 1.2 ; 1.6 ; 2.0 ; 2.4 TIG —wires(mm): 1.6 ; 2.0 ; 2.4 ; 3.2 ; 4.0 ; 5.0 ; 6.0 |
wire Packagings |
Mig wires : S100/0.5kg 1Lb , S200/2kg , S270-S300/6kg-7kg |
Tig wire ) : 5/10kg ······· length :1000mm |
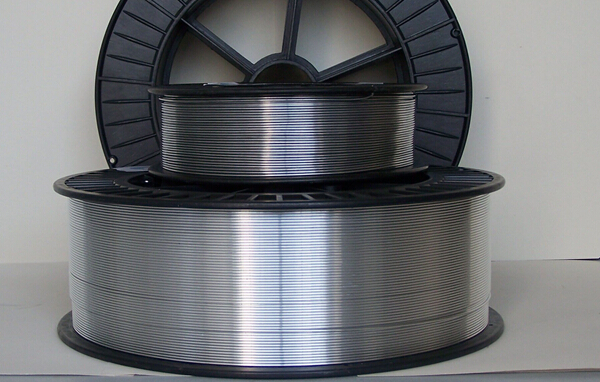
Note:
1. Electwiree is extremely easy to be affected with damp, so should be stored in dry sealed containers,
in order to prevent damp metamorphism.
in order to prevent damp metamorphism.
2. Before welding, the welding wire is about 150 degrees Celsius for 1-2 hours.
3. Should be welded by plate, and to 200--300 degrees after welding according to the thickness of heating
welding. Welding process, the welding wire does not do the lateral swing, in order to improve the welding speed,
welding electwiree should be perpendicular to the surface, the arc should be as short as possible. Replacement
of electwiree must be carried out quickly.
welding. Welding process, the welding wire does not do the lateral swing, in order to improve the welding speed,
welding electwiree should be perpendicular to the surface, the arc should be as short as possible. Replacement
of electwiree must be carried out quickly.
4. The welding parts must be clear before welding, impurities. After welding should carefully clear slag, and use
steam or hot water washed clean.
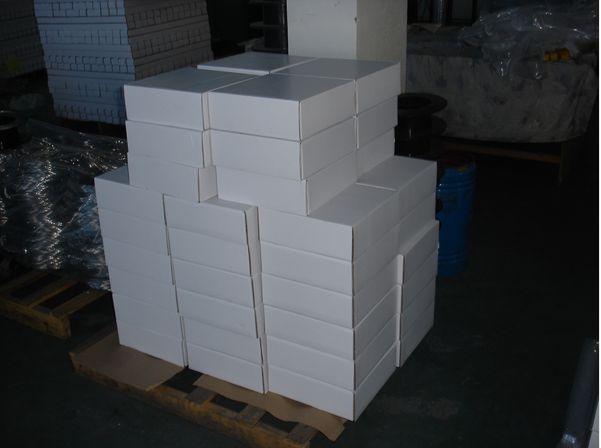
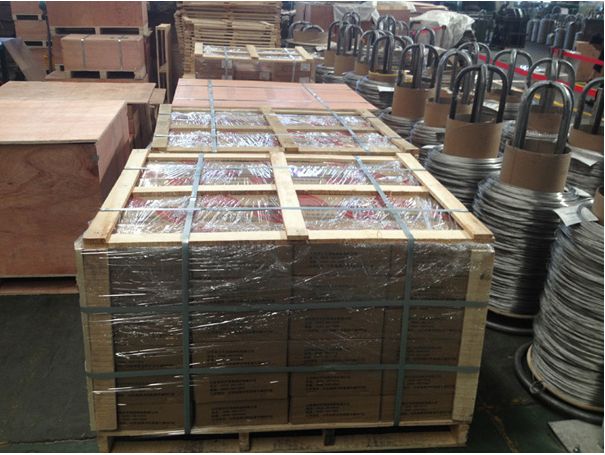
steam or hot water washed clean.
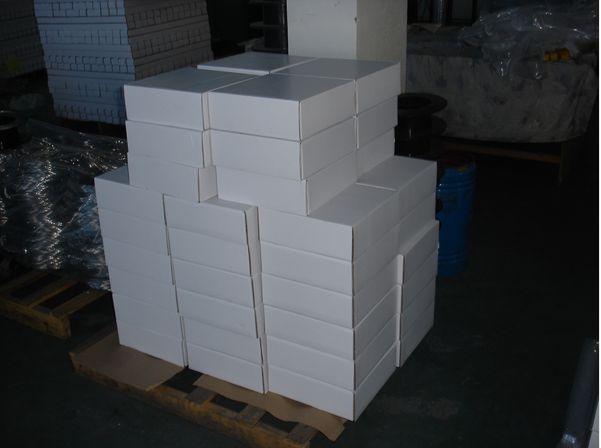
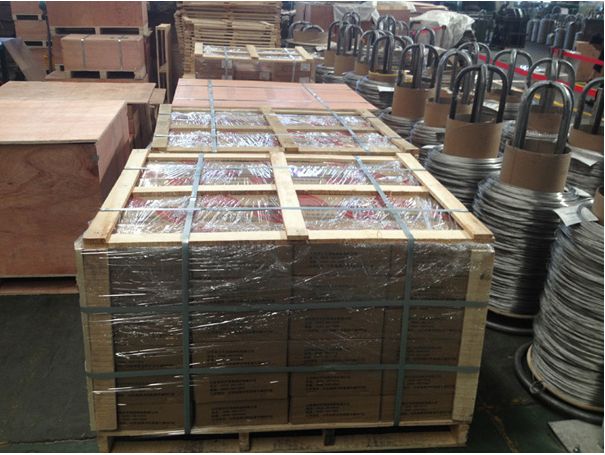