ER5556 aluminum MIG welding wire
Author: Time:2023-05-17
ER5556 aluminum magnesium welding wire with higher than 5% mg and high manganese content, has high strength, good corrosion resistance and thermal cracking resistance. After the welding of the welding seam is still white, it can provide a good color for the welded joint.
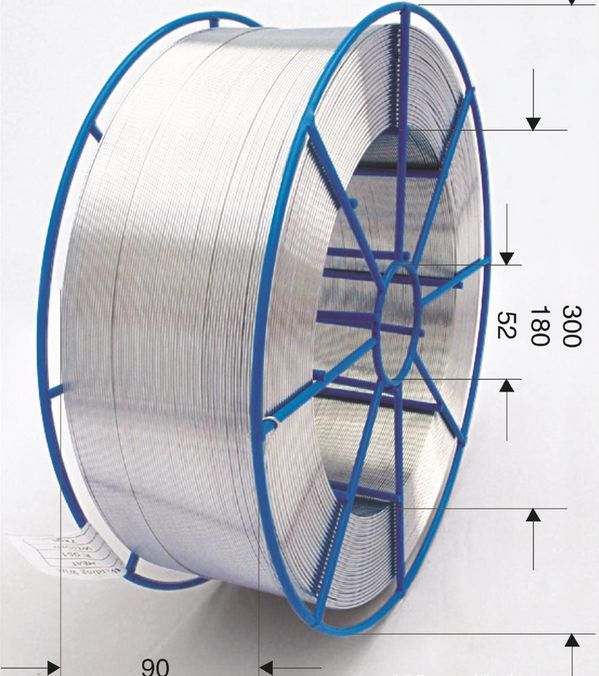
Purpose: for high magnesium (3%Mg) aluminum alloy argon arc welding of filling material.
Physical Property | ||||
---|---|---|---|---|
Density kg/dm3 |
Melting temperature ℃ |
Thermal conductivity w/m•K |
Linear expansion coefficient 10¯6/K(20-100℃) |
Electric conductivity % IACS |
2.65 | 572-633 | 116 | 23.9 | 29 |
Weld Mechanical Properties (reference value) | ||
---|---|---|
Tension Strength(MPa) | Yield Strength(MPa) | Elongation (%) |
280--310 | 130--140 | 15--20 |
ER5556 Aluminium & Aluminium Alloy welding wires | |
Classification | GB/T 10858-2008 AWS A5.10····· ER5556 |
Typical composition in % |
Si··················· <0.25 Fe··················· <0.40 Cu··················· <0.10 Mn················· 0.60—1.00 Mg················· 4.70—5.50 Cr················· 0.05—0.20 Zn··················· <0.20 Be·················· <0.0003 Ti················· 0.05—0.20 Others··············· <0.05 Others Total··········· <0.15 |
Physical properties (Approx.Values) |
0.2% yield strength Rpo2 (Mpa)···· 125 Tensile Strength Rm (Mpa)····· 275 Elongation A5 (L0=5d0) (%)······ 17 Test Temperature (℃)······ 20 |
Performance & Usage |
This type of pwireuct has good performance in mechanics widely used in welding joint with special requirement of higher intensity。 Pwireuct Usage:like engine, electric, power,chemistry, and food etc. |
Shielding gas |
Argon, Helium, or Argon/Helium—mixtures. |
Dimensions Φ |
MIG—wires (mm): 0.8 ; 0.9 ; 1.0 ; 1.2 ; 1.6 ; 2.0 ; 2.4 TIG —wires(mm): 1.6 ; 2.0 ; 2.4 ; 3.2 ; 4.0 ; 5.0 ; 6.0 |
wire Packagings |
Mig wires: S100/0.5kg 1Lb , S200/2kg , S270-S300/6kg-7kg |
Tig wire : 5/10kg ······· length :1000mm |
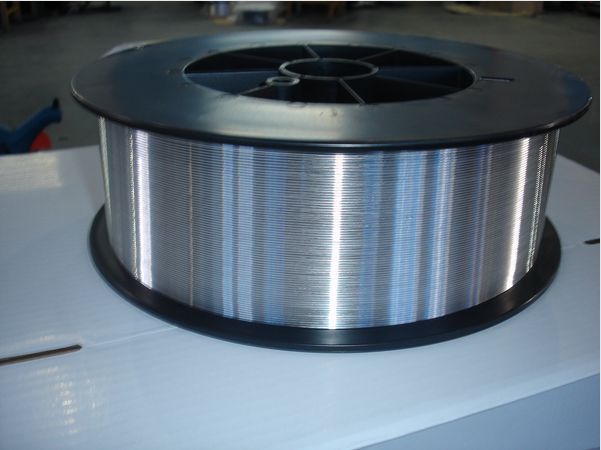
Note:
1. The welding wire is not used in the structure of aluminum alloy, which is more than 65 degrees, because in
the above mentioned temperature, the stress corrosion cracking of the welded joints.
the above mentioned temperature, the stress corrosion cracking of the welded joints.
2. Welding should be strict and clear the edge of the welding of the oxide film and oil, otherwise it will cause
welding seam welding and cause the hole, slag and other defects.
welding seam welding and cause the hole, slag and other defects.
3. Welding can be used for holding molten metal plate, in order to ensure the weld forming, and avoid hot crack.
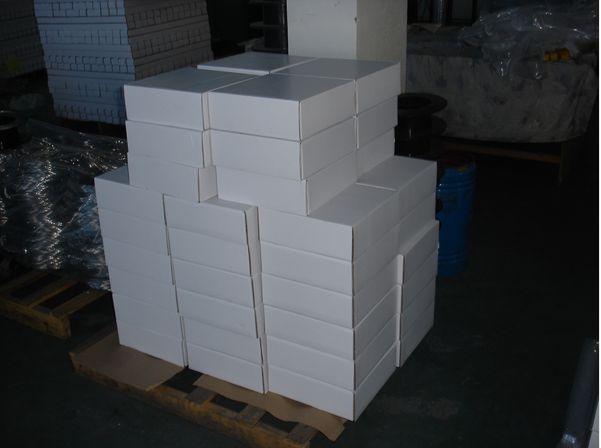
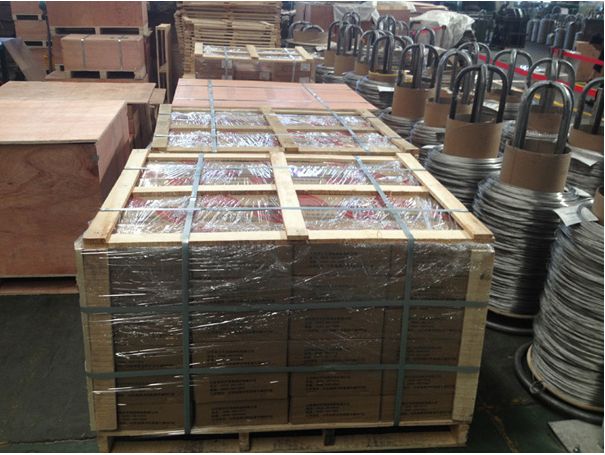
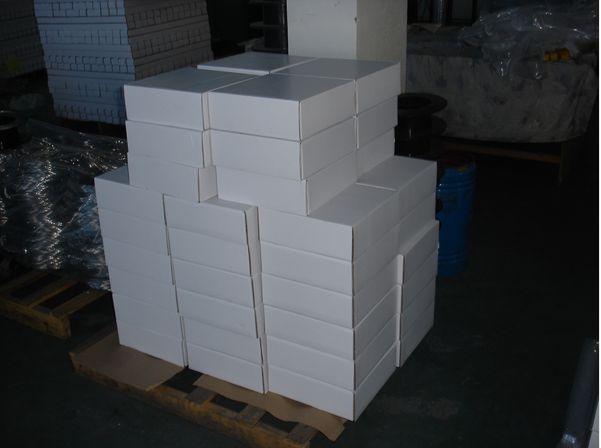
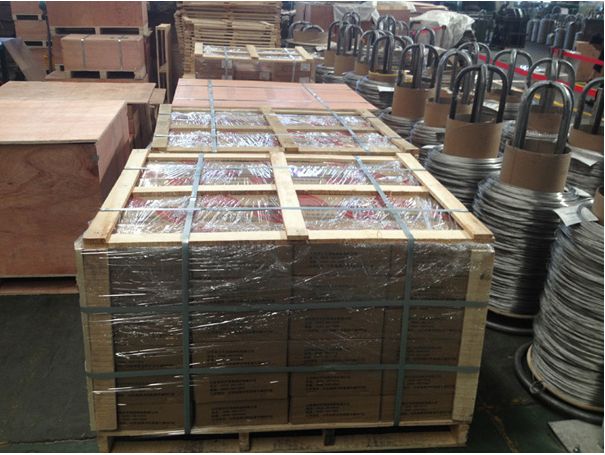